5 problemas eléctricos en tus equipos de producción que debes evitar cuando usas variadores de velocidad
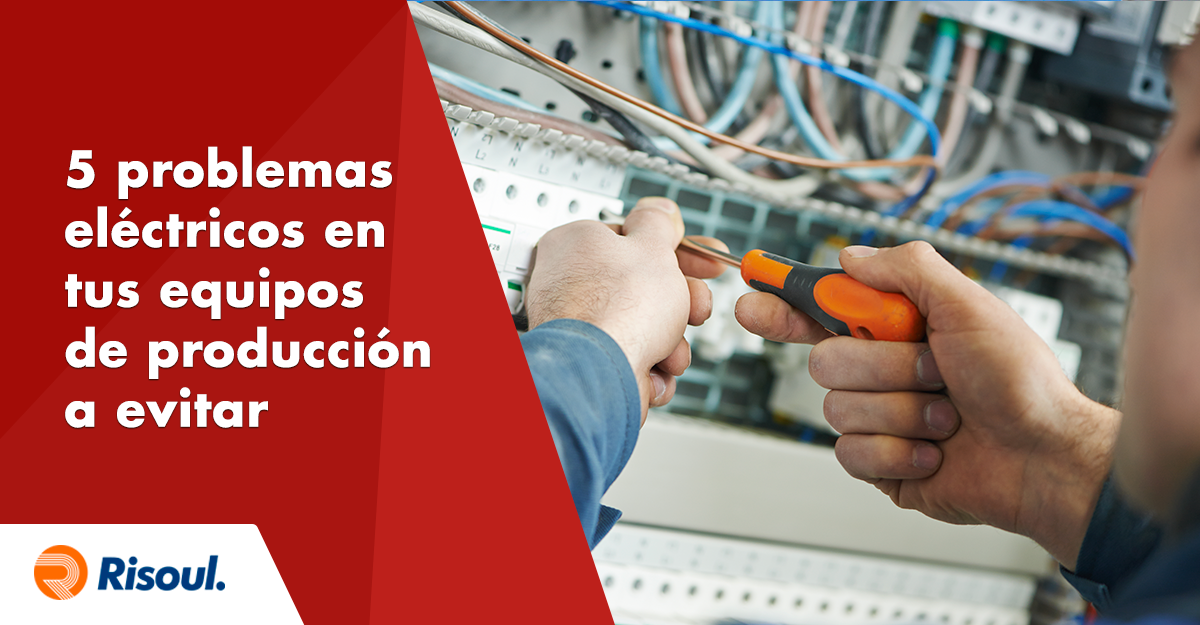
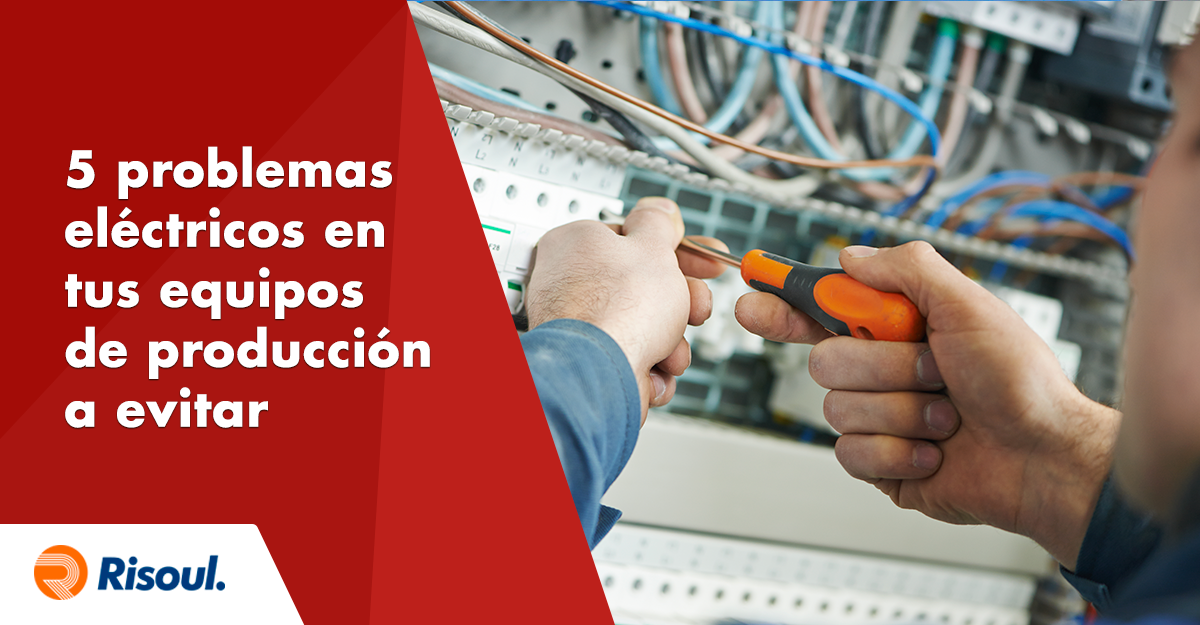
Los diferentes tipos de industria como papelera, automotriz, minera, metalúrgica, de alimentos, del cuidado de la salud, cementera, etc; se enfrentan a grandes desafíos durante su operación diaria.
Uno de ellos son los paros imprevistos y averías generadas por diversos problemas eléctricos que pegan directamente en la producción.
Conoce los 5 problemas eléctricos más comunes en tus procesos y cómo puedes prevenirlos.
Contenidos de este artículo:
Problema #1: Armónicos
Problema #2: Aplicaciones con alta regeneración
Problema #3: Rendimiento de la aplicación
Problema #4: Calidad del producto final
Problema #5: Tiempos improductivos de equipos
Problema #1: Armónicos
¿Que tipo de problemas se tienen por la presencia de armónicos?:
- Desperdicio de energía
- Saturación de transformadores
- Daños en equipos electrónicos (tarjetas o componentes)
- Disparos inexplicables de Breakers
- Aperturas de fusibles sin razón lógica
- Pérdida de la programación/configuración de equipos, etc
Solución: El uso de filtros contra armónicos marca MTE cuando se usan variadores de velocidad permite reducir al mínimo la presencia de armónicos cumpliendo con el estándar IEEE 519. Estos filtros se pueden colocar en nuevos proyectos con variadores o en equipos existentes. Este tipo de filtro es externo al variador de velocidad y de hecho puede ser usado con la diferentes marcas de variadores que existen en el mercado.
Otra opción es usar variadores de velocidad que ya tiene integrado el filtro contra armónicos como el modelo PowerFlex 755TL de Allen Bradley/Rockwell Automation. Este equipo también cumple con el estándar IEEE 519.
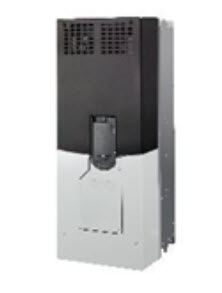
Problema #2: Aplicaciones con alta regeneración
Existen aplicaciones en las que el motor regresa una gran cantidad de energía hacia el variador de velocidad(en caso que el variador sea el tipo de arranque que se use), dicha energía daña al equipo a grandes rasgos porque los componentes electrónicos reciben un voltaje más alto de lo fueron diseñados.
Una forma de controlar esto es con el frenado dinámico, sin embargo esta solución propicia grandes desperdicios de energía para el caso en cuestión de una aplicación con mucha regeneración, ya que la energía excesiva(regeneración) es quemada en forma de calor en un resistor.
Solución: El modelo PowerFlex 755TR de Allen Bradley permite regresar esta energía a la línea de alimentación gracias a su tecnología de Frente Activo (AFE=Active Front End), brindando importantes ahorros de energía. Esto no lo puede hacer el frenado dinámico que sólo quema la energía excesiva en forma de calor a través de un resistor o banco de resistores.
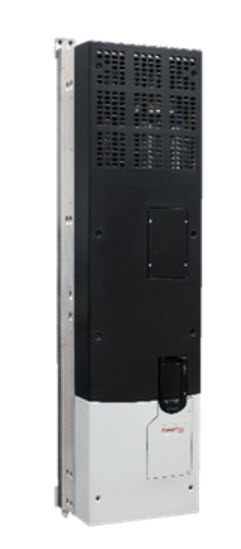
Problema #3: Rendimiento de la aplicación
Existen aplicaciones en donde se presentan cambios de cargas en el funcionamiento del equipo. Esto provoca que esta maquinaria trabaje de forma inestable y ocurren en determinado momento detenciones inesperadas en las líneas de producción.
Solución: Con la tecnología de control adaptivo del Powerflex 755T se evitan detenciones por cambios de carga, a grandes rasgos porque esta tecnología implementa sintonizaciones automáticas en dichas condiciones permitiendo que el equipo siga funcionando.
Problema #4: Calidad del producto final
Durante la operación pueden ocurrir variaciones en la alimentación, tales como:
- Picos de voltaje
- Parpadeos
- Apagones
- Variaciones de voltaje, etc
Estas variaciones pueden afectar el desempeño de los equipos e impactar negativamente la calidad del producto final.
Solución: Con el control adaptivo de Powerflex 755T este tipo de variaciones en la línea de alimentación es compensado internamente con el Observador del Bus junto con el control adaptativo de los equipos para así evitar una disminución en la calidad del producto final.
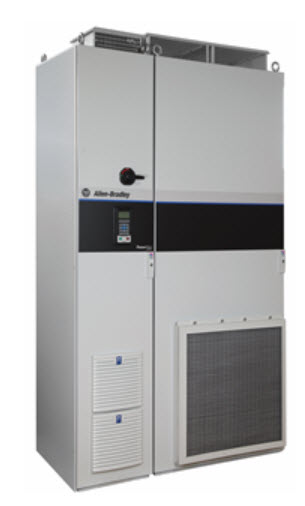
Problema #5: Tiempos improductivos de equipos
Gran parte de los paros en planta ocurren debido a la falta de información necesaria para evitar tiempos muertos.
Solución: Powerflex 755T brinda con información sobre los indicadores que permitirán evitar tiempos muertos, tales como:
- Tiempo de vida esperado de los ventiladores
- Tiempo de vida estimado de los IGBTs
- Vida útil estimada de las salidas relevador
- Cuándo es necesario hacer el mantenimiento del motor
- Temperaturas en las diferentes secciones del variador, etc
En Risoul somos expertos en automatización y contamos con el respaldo de marcas expertas como Rockwell Automation. Acércate a nuestros asesores para conocer la solución más adecuada para tu planta industrial.
{{cta('5d0f71da-18da-4de2-9cb5-fb8ae5f1def6')}}
Suscríbete al boletín
Recibe información de nuestras marcas, promociones, eventos ¡y más!